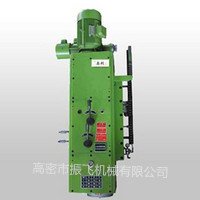
高密市振飛機(jī)械制造有限公司
經(jīng)營模式:生產(chǎn)加工
地址:山東高密市夏莊鎮(zhèn)河西村
主營:鏜銑頭,銑頭,動力銑頭,數(shù)控銑頭,直角銑頭,萬向銑頭
業(yè)務(wù)熱線:0536-2758966
山東鉆孔動力頭-高密振飛機(jī)械-鉆孔動力頭定做
鏜銑頭,銑頭,數(shù)控銑頭
動力頭說明
?。薄⒉灰贈]有開啟冷卻液的情況下使用,內(nèi)部油封可能快速磨損;
?。病楸苊鈩恿Φ蹲鶅?nèi)部機(jī)件過度磨損或油封損壞,冷卻液需要有適當(dāng)?shù)倪^濾裝置;
?。?、不可超過刀座額定**大轉(zhuǎn)速;
?。?、不可超過刀座**大容許水壓;
5、使用刀具為有中心出水刀具;
6、需搭配止水筒夾及止水螺帽使用;
?。贰⑹褂们按_認(rèn)內(nèi)外部噴水處無阻塞;
?。?、運(yùn)轉(zhuǎn)前需先供水避免過熱;
?。埂⒅恍柚行某鏊畷r可將外部噴水關(guān)閉;
10、關(guān)閉外部出水時,將外部噴水處使用螺絲將其封閉。






攻絲動力頭絲錐斷裂的原因有哪些?
1、攻絲步驟不當(dāng)。對高硬度的攻件或深孔進(jìn)行攻絲時,應(yīng)分級攻絲,避免一氣呵成。
2、絲錐焊接不良。尤其是大規(guī)格的絲錐,不少生產(chǎn)商為節(jié)省昂貴的高速鋼,絲錐柄、刃分別采用45鋼與高速鋼經(jīng)摩擦對焊而成。大量的絲錐斷裂是由于焊接不牢造成的。絲錐的焊接質(zhì)量主要由焊接摩擦壓力、摩擦?xí)r間、頂鍛壓力及頂鍛時間決定。摩擦階段要使45鋼和高速鋼接觸面上的低熔點(diǎn)化合物等有害雜質(zhì)都被擠出,后在適當(dāng)?shù)捻斿憠毫ο聰D壓在一起。 焊接時,由于45鋼在高溫下強(qiáng)度很低,在摩擦壓力下會產(chǎn)生很大的壓縮變形,形成很大的翻邊;而高速鋼由于有足夠強(qiáng)度使翻邊很小,這就使待焊表面高速鋼一側(cè)的低熔點(diǎn)化合物未被完全擠出,焊后容易產(chǎn)生裂紋,在絲錐使用過程中裂紋擴(kuò)展造成斷裂。 此外,絲錐焊接后如果消除應(yīng)力不及時,也很容易在熱影響區(qū)產(chǎn)生斷裂。
3、絲錐有效截面積過小,導(dǎo)致單位截面積承載力過大,超過絲錐強(qiáng)度極限時發(fā)生的斷裂
4、絲錐截面過渡處尺寸差別太大或沒有設(shè)計(jì)過渡圓角導(dǎo)致應(yīng)力集中,使用時易在應(yīng)力集中處發(fā)生斷裂。柄、刃交界處的截面過渡處離焊口距離太近,導(dǎo)致復(fù)雜的焊接應(yīng)力與截面過渡處的應(yīng)力集中相迭加,產(chǎn)生較大的應(yīng)力集中,導(dǎo)致絲錐在使用中斷裂。
5、絲錐選擇不當(dāng)。對硬度太大的攻件應(yīng)該選用高品質(zhì)絲錐,如含鈷材料絲錐、硬質(zhì)合金絲錐、涂層絲錐等
6、熱處理工藝不當(dāng)。絲錐熱處理時,若淬火加熱前不經(jīng)預(yù)熱、淬火過熱或過燒、不及時回火及清洗過早都有可能導(dǎo)致絲錐產(chǎn)生裂紋。
動力頭的常見故障分析及解決方案(二)
動力頭是我公司的主營產(chǎn)品之一,其出廠前必須經(jīng)過嚴(yán)格的性能檢驗(yàn),合格之后方可出廠。但是,在組裝專機(jī)并與相關(guān)設(shè)備連接時,或在連續(xù)運(yùn)轉(zhuǎn)中發(fā)生不良動作時,請務(wù)必切斷電源和氣源。以下是動力頭不進(jìn)給或不能平滑的進(jìn)給故障原因分析及解決方案:
原因:
1、供給不足、量不足
2、固定鉆削動力頭的夾緊支架的位置不良、或夾緊螺栓擰的過緊
3、鉆削動力頭的安裝精度差,進(jìn)給時,鉆頭產(chǎn)生扭曲
4、液壓式阻尼器的調(diào)節(jié)閥呈關(guān)閉狀態(tài)
5、進(jìn)給的壓力氣中水分含有量大,增加了滑動部的阻尼
6、前進(jìn)及后退時,移動的部分與其他固定件件接觸或發(fā)生碰撞
解決方案:
1、檢查、調(diào)查后設(shè)定標(biāo)準(zhǔn)值(0.5~0.6Mpa)
2、請將支架安裝在規(guī)定的范圍內(nèi),并按適當(dāng)?shù)呐ぞ財Q緊固定螺栓
3、檢查調(diào)節(jié)安裝精度(適用鉆頭套和導(dǎo)軌夾具時需特點(diǎn)注意)
4、調(diào)節(jié)液壓阻尼器的調(diào)節(jié)旋鈕,設(shè)定適當(dāng)?shù)倪M(jìn)給速度
5、在空氣壓縮機(jī)出口部安裝冷卻裝置,或在管路中安裝濾水網(wǎng)以清除水份,如水份大量侵入,則鉆削動力頭需要修理
6、調(diào)整位置,避免接觸或碰觸